Understanding and Managing Power Quality in Industrial Systems
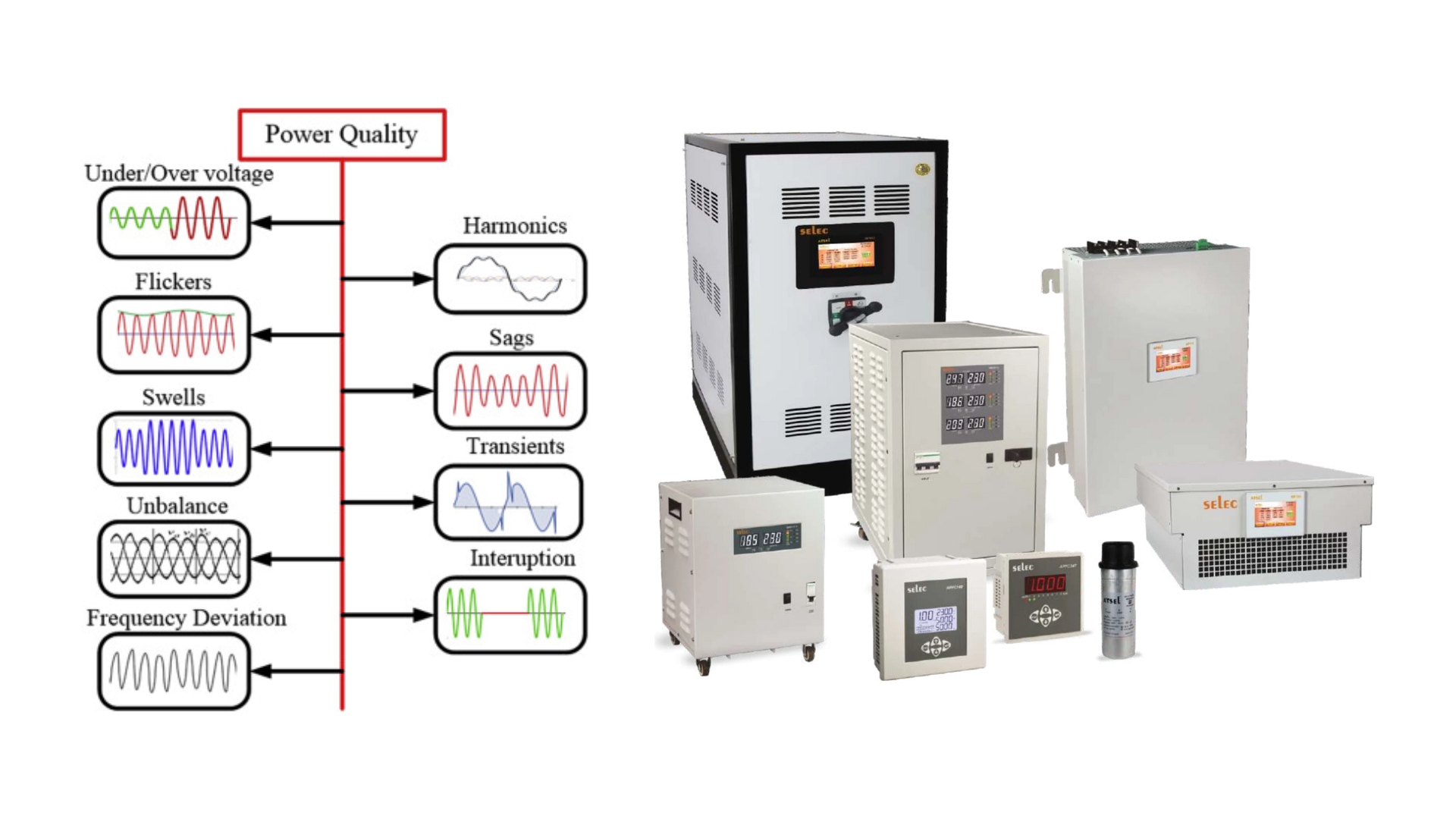
In today’s industrial environments, where automation, sensitive electronics, and high-energy processes coexist, power quality is no longer just a utility-side concern — it’s a frontline operational issue.
Unexpected tripping, overheating, capacitor bank failures, and even premature aging of drives and control panels are often symptoms of deeper, invisible problems in the electrical supply. This article explores how poor power quality impacts operations, the types of disturbances involved, and practical methods to detect and manage them effectively.
What Is Power Quality?
Power quality refers to the characteristics of voltage and current waveforms that power your equipment. Ideal power is a smooth sinusoidal waveform at stable voltage and frequency. However, real-world systems often experience distortions, imbalances, and fluctuations that compromise performance.
Good power quality ensures that electrical equipment operates reliably and efficiently. Poor power quality can lead to reduced lifespan, increased maintenance, and operational disruptions.
Common Power Quality Issues
1. Voltage Imbalance
Occurs when the voltages on a three-phase system are not equal in magnitude or phase. Even minor imbalance (<2%) can increase current draw, heat motors, and degrade insulation.
2. Harmonics
Generated by non-linear loads such as drives, inverters, and LED lighting. Harmonics distort the sinusoidal waveform and contribute to:
- Overheating of transformers and cables
- False tripping of protection devices
- Increased I2R losses and energy waste
3. Voltage Dips and Swells
Momentary drops or rises in voltage caused by sudden load changes or grid issues. These can lead to PLC resets, controller failures, and shutdowns.
4. Flicker
Rapid fluctuations in voltage that cause lighting instability and strain on sensitive equipment.
5. Neutral Current Rise
An effect of phase imbalance and harmonic distortion, especially in systems with high single-phase loads, leading to transformer heating and reduced power efficiency.
6. Poor Power Factor
A lagging power factor due to inductive loads results in higher kVA demand, utility penalties, and underutilization of infrastructure.
Why It Matters
Poor power quality affects not just electrical parameters, but core operational efficiency:
- Downtime due to unexpected tripping
- Faster degradation of motors and drives
- Excess heat in panels and cables
- Unpredictable behavior in automation systems
- Shortened life of control gear and instrumentation
All of these translate into higher energy costs, reduced productivity, and more frequent maintenance interventions.
Real-World Examples
- A forging unit experiences frequent contactor burns due to voltage imbalance.
- A dairy plant faces capacitor bank failures every few months due to harmonics.
- A commercial building logs frequent UPS alarms because of neutral shifting.
- A textile unit’s variable frequency drives (VFDs) repeatedly trip without visible faults — traced back to harmonic distortion.
Detection: Monitoring Is Key
To manage power quality, the first step is measuring it accurately. Intelliware supports industrial facilities with field-tested products for monitoring and detection:
Multifunction Meters with PQ Features
Devices like SELEC MFM384 or Elmeasure MFM+ offer real-time monitoring of:
- Total Harmonic Distortion (THD)
- Power factor
- Voltage/current imbalance
- Frequency deviations
Power Quality Analyzers
Class-A analyzers log waveform data over time and provide trend analysis and alerts.
IoT-Based Monitoring Platforms
These allow real-time dashboards, auto-reporting, and remote access to PQ parameters for predictive maintenance.
Solutions: Managing Power Quality
1. Active & Static VAR Generators (ASVG/SVR)
ASVGs dynamically inject reactive power and cancel harmonics in real-time. Ideal for variable loads and installations with stringent PF and THD limits.
2. Advanced Harmonic Filters
Passive or hybrid filters target specific harmonic orders and protect downstream devices from waveform distortion.
3. Power Factor Correction Controllers
SELEC and Elmeasure APFC controllers automate capacitor bank switching to maintain PF within acceptable limits, reducing utility penalties.
4. System Redesign and Load Management
Reconfiguring loads across phases, balancing single-phase devices, and upgrading cables or isolators to reduce imbalance and overheating.
Conclusion
Power quality isn’t a luxury metric — it’s a core operational parameter. Addressing it can lead to:
- More stable systems
- Lower energy losses
- Extended asset life
- Fewer unplanned shutdowns
If you’re facing unexplained electrical disturbances or want to assess your system for hidden inefficiencies, now is the time to start monitoring.
Let Intelliware help you make power visible, reliable, and efficient.