Power Quality Devices: Enhance Energy Efficiency & Reduce Carbon Footprint
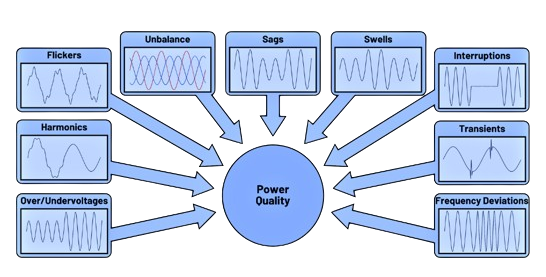
In today’s industrial landscape, efficiency, reliability, and sustainability are key drivers of success. The performance of electrical systems plays a critical role in ensuring that industrial operations run smoothly and efficiently. However, the quality of power supplied to industrial facilities is often overlooked, leading to inefficiencies, equipment damage, and increased operational costs. This is where power quality devices come into play. These devices not only enhance the reliability of industrial processes but also contribute significantly to sustainability by reducing energy waste and lowering the carbon footprint.
Understanding Power Quality
Before diving into the role of power quality devices in industrial settings, it’s important to understand what power quality means. Power quality refers to the stability and purity of the electrical power supplied to equipment. It encompasses factors like voltage levels, frequency stability, harmonic distortion, and the presence of transients or interruptions. Poor power quality can lead to a host of issues, including equipment malfunctions, energy inefficiencies, and even safety hazards.
The Importance of Power Quality in Industrial Settings
Industries rely heavily on complex machinery and sensitive equipment that require consistent and clean power to function optimally. Poor power quality can disrupt operations, cause equipment to fail prematurely, and lead to costly downtime. For example, voltage sags, swells, or interruptions can halt production lines, while harmonic distortions can cause overheating in motors and transformers.
In addition to operational challenges, poor power quality can lead to significant energy inefficiencies. For instance, low power factor (a common power quality issue) results in increased energy consumption, higher electricity bills, and a larger carbon footprint. As industries strive to become more sustainable and energy-efficient, addressing power quality issues becomes essential.
What Are Power Quality Devices?
Power quality devices are specialized equipment designed to monitor, analyze, and correct power quality issues in electrical systems. These devices help maintain the stability and integrity of power supplied to industrial equipment, ensuring optimal performance and efficiency.
Types of Power Quality Devices
There are several types of power quality devices, each designed to address specific issues. Some of the most common types include:
- Voltage Regulators: These devices maintain consistent voltage levels, preventing voltage sags, swells, and fluctuations that can damage equipment.
- Harmonic Filters: Harmonic distortions, caused by non-linear loads such as variable speed drives and rectifiers, can lead to overheating and equipment failure. Harmonic filters reduce these distortions, ensuring clean power supply.
- Uninterruptible Power Supplies (UPS): UPS systems provide backup power during outages and protect against power interruptions, ensuring continuous operation of critical equipment.
- Surge Protectors: These devices protect equipment from voltage spikes or surges, which can cause immediate or cumulative damage to sensitive electronics.
- Power Factor Correction (PFC) Units: PFC units improve power factor by reducing reactive power, leading to more efficient energy use and lower electricity bills.
- Transient Voltage Surge Suppressors (TVSS): These protect against transient over-voltages that can damage equipment or disrupt operations.
- Dynamic Voltage Restorers (DVR): DVRs correct short-term voltage sags and swells, ensuring continuous voltage supply to sensitive equipment.
Installation and Integration in Industrial Settings
Power quality devices can be installed at various points within an industrial electrical system, depending on the specific needs of the facility. Common installation points include:
- Service Entrance: Installing power quality devices at the service entrance protects the entire facility from external power quality issues such as voltage sags or surges from the grid.
- Sub-Panels or Distribution Boards: This allows for targeted protection of specific areas within the facility, such as production lines or data centers.
- Close to Sensitive Equipment: Directly installing power quality devices near sensitive equipment ensures maximum protection and reliability for critical processes.
Integration of power quality devices into an industrial facility requires careful planning and analysis. A comprehensive power quality audit is often the first step, identifying existing issues and determining the appropriate devices for remediation.
Applications in Industrial Operations
Power quality devices have a wide range of applications across various industrial sectors. Some of the most common applications include:
- Manufacturing: In manufacturing plants, power quality devices ensure that production lines run smoothly without interruptions or equipment failures. This is particularly important in industries such as automotive, electronics, and pharmaceuticals, where precision and reliability are critical.
- Data Centers: Data centers rely on clean, uninterrupted power to ensure the integrity of data and the smooth operation of servers. Power quality devices such as UPS systems and harmonic filters are essential to prevent downtime and data loss.
- Oil & Gas: In the oil and gas industry, power quality devices help maintain the reliability of drilling and extraction equipment, preventing costly downtime and ensuring safety in hazardous environments.
- Food & Beverage: Consistent power quality is crucial for maintaining the integrity of refrigeration, processing, and packaging equipment in the food and beverage industry.
- Textiles: The textile industry uses power quality devices to protect machinery like looms, dyeing machines, and spinning machines from voltage fluctuations and harmonics.
Benefits of Installing Power Quality Devices
The installation of power quality devices in industrial settings offers numerous benefits, including:
- Increased Equipment Lifespan: By providing stable and clean power, these devices reduce the wear and tear on equipment, extending its lifespan and reducing maintenance costs.
- Energy Efficiency: Power quality devices such as power factor correction units and harmonic filters improve the efficiency of electrical systems, reducing energy consumption and lowering electricity bills.
- Cost Savings: Improved power quality leads to fewer equipment failures, reducing downtime and the associated costs. Additionally, energy savings contribute to lower operational expenses.
- Enhanced Reliability: Ensuring consistent power quality reduces the risk of unexpected shutdowns and disruptions, leading to more reliable operations and improved productivity.
- Sustainability: By reducing energy waste and improving efficiency, power quality devices contribute to lower carbon emissions, helping industries meet their sustainability goals.
Risks Managed and Avoided by Power Quality Devices
Power quality devices help manage and avoid several risks that can have serious implications for industrial operations, including:
- Equipment Damage: Voltage spikes, sags, and harmonic distortions can cause significant damage to sensitive equipment. Power quality devices protect against these issues, preventing costly repairs or replacements.
- Operational Interruptions: Poor power quality can lead to unexpected shutdowns and production delays. Power quality devices ensure continuous operation, minimizing downtime and maintaining productivity.
- Safety Hazards: Power quality issues can increase the risk of electrical fires, particularly in environments with flammable materials. By stabilizing power supply, power quality devices reduce this risk.
- Compliance Risks: Many industries are subject to strict regulatory standards for energy efficiency and emissions. Power quality devices help facilities meet these standards, avoiding potential fines and penalties.
Leading Manufacturers of Power Quality Devices in India
India is home to several leading manufacturers of power quality devices, providing a wide range of solutions for industrial applications. Some of the top manufacturers include:
- Schneider Electric: A global leader in energy management and automation, Schneider Electric offers a comprehensive range of power quality devices, including voltage regulators, UPS systems, and harmonic filters.
- Siemens: Siemens provides advanced power quality solutions for industrial applications, including power factor correction units and dynamic voltage restorers.
- L&T (Larsen & Toubro): L&T offers a variety of power quality devices designed for industrial environments, including surge protectors, harmonic filters, and voltage regulators.
- ABB: ABB is known for its innovative power quality solutions, including UPS systems, power factor correction units, and transient voltage surge suppressors.
- SELEC: SELEC controls provides a wide range of power quality devices, including harmonic filters, voltage regulators, and power factor correction systems.
- Elmeasure: Elmeasure offers reliable and cost-effective power quality devices for industrial applications, including power quality aanalyzers and monitors etc.
- Eaton: Eaton specializes in power management solutions, including power quality devices like UPS systems, voltage regulators, and harmonic filters.
Electrical Standards for Power Quality Devices
Power quality devices must adhere to specific electrical standards to ensure safety, reliability, and performance. Some of the key standards include:
- IEC 61000 Series: This series of standards covers electromagnetic compatibility (EMC) and power quality, ensuring that devices do not cause harmful interference and can operate effectively in various environments.
- IEEE 519: The IEEE 519 standard provides guidelines for harmonic control in electrical power systems, helping to minimize harmonic distortion and improve power quality.
- IS 732:2019: This Indian standard outlines the code of practice for electrical wiring installations, including guidelines for the installation of power quality devices.
- IS 13234: This standard focuses on power quality in low-voltage distribution networks, providing guidelines for the design and implementation of power quality solutions.
How Power Quality Devices Contribute to Energy Efficiency and Sustainability
Power quality devices play a crucial role in enhancing energy efficiency and promoting sustainability in industrial operations. Here’s how:
- Reducing Energy Losses: Power factor correction units and harmonic filters reduce reactive power and harmonic distortions, leading to more efficient energy use and lower energy losses.
- Optimizing Equipment Performance: By providing stable and clean power, power quality devices ensure that equipment operates at optimal efficiency, reducing unnecessary energy consumption.
- Lowering Carbon Emissions: Reduced energy consumption directly translates to lower carbon emissions, helping industries reduce their carbon footprint and contribute to climate action.
- Supporting Renewable Energy Integration: Power quality devices can help manage the variability and intermittency of renewable energy sources, ensuring stable power supply and supporting the transition to clean energy.
Impact on Sustainable Development Goals (SDGs)
The installation of power quality devices in industrial operations aligns with several Sustainable Development Goals (SDGs), including:
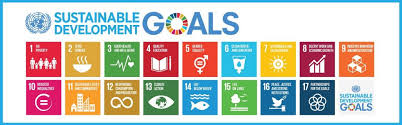
- SDG 7: Affordable and Clean Energy: Power quality devices contribute to more efficient energy use, making energy more affordable and accessible while supporting the transition to clean energy.
- SDG 9: Industry, Innovation, and Infrastructure: By improving the reliability and efficiency of industrial operations, power quality devices enhance the resilience and sustainability of infrastructure.
- SDG 12: Responsible Consumption and Production: Power quality devices promote responsible energy consumption by reducing energy waste and optimizing resource use.
- SDG 13: Climate Action: By lowering energy consumption and carbon emissions, power quality devices support efforts to combat climate change and mitigate its impacts.
Conclusion
Power quality devices are essential tools for ensuring the reliability, efficiency, and sustainability of industrial operations. By addressing power quality issues, these devices protect critical equipment, reduce energy waste, and contribute to lower operational costs. Moreover, they play a significant role in helping industries meet their sustainability goals, particularly in the context of energy efficiency and carbon reduction. As industries continue to evolve and prioritize sustainability, the adoption of power quality devices will become increasingly important, paving the way for more resilient and sustainable industrial operations.